Sensing for Welding Technology
Welding Sensors Make Sense
Over time, there was a need to create smarter systems capable of delivering higher efficiency, fewer errors, and lower cycle times. As a result, welding and robotic processes have improved dramatically. Besides, manufacturing industries are deploying industrial robots at an exponential rate to reduce operating costs and increase profit margins.
Industrial development requires advances in technology. For welding, this new technology is most popularly achieved through a variety of sensor technologies that have brought welding automation to the next level.
Different Types of Sensors
Sensors are used specifically for robotic welding applications, generally divided into four categories: induction, through-arc, laser and visual. Likewise, they have three main functions: seam finding, seam tracking and/or partial scanning, which can also be used for inspection.
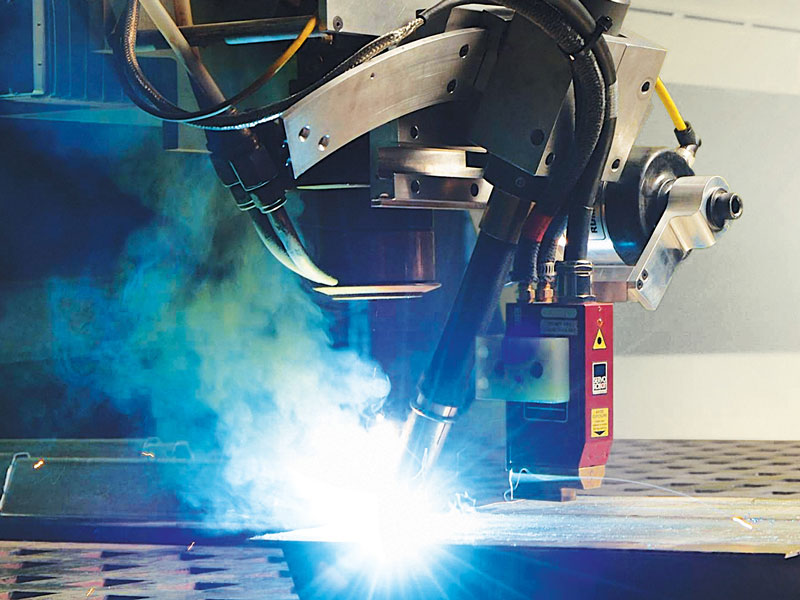
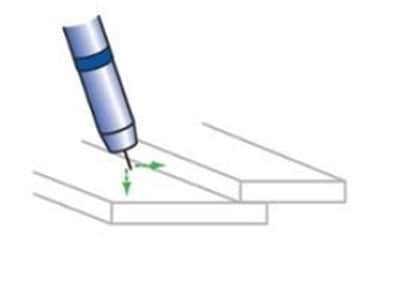
Wire Touch Sense
Touch, is the physical sensation of the solder wire from the end of the torch to detect the conductive surface of the part to be soldered.
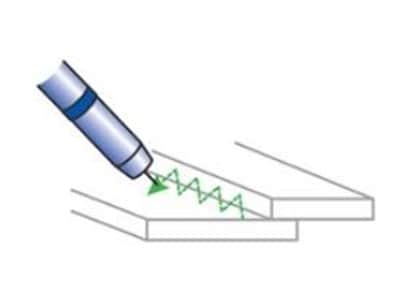
Through-Arc Seam Tracking
Advanced technology that uses sensors mounted near the welding power source to actively measure arc characteristics in the weld to identify variations between the robot's taught path and the actual weld.
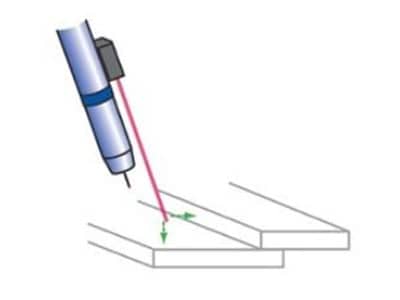
Laser Sensing
The laser sensor is a non-contact option. Instead of physically touching a surface with a wire, a laser dot and sensor record the position and orientation of a part rapidly as the laser is fired.
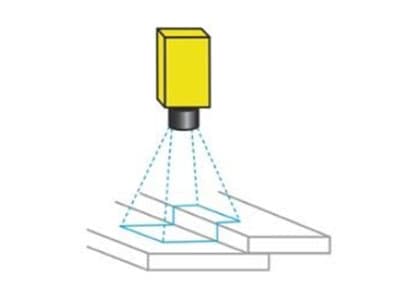
2D Camera
Camera systems, which allow the user to capture the position of a plane in just one second using a camera sensor attached to the robot's arm. This system not only finds the position of the joint, but also quickly confirms the orientation without adding as many check points as required by touch sensor or laser sensor.
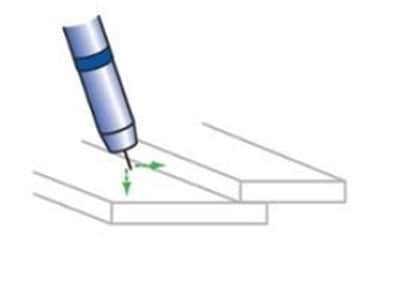
Laser Seam Tracking
When the latest technology laser sensors are combined with a high-speed controller, weld and part positions can be processed in real time. Like solutions that compensate for the path and even adjust the welding parameters for the position and variation of the weld.
When do Sensors Make Sense?
If a product with variations that tooling and product consistency, or design, cannot deal with, a sensor solution is needed. Note that ROI expectations should be set with clear goals related to the investment (reduce waste, improve quality, reduce downtime, improve production, etc…). While the initial cost of deploying robots may seem overwhelming for some manufacturers, understanding the cost savings associated with a long-term approach to automation – and next technologies, like sensor – is essential. Return on investment is usually realized quickly aside from sticker shock and should be discussed in more detail with an automation integrator. Moreover, education about the different types of sensors (and their capabilities) available for advanced robotic welding solutions will make it easier for manufacturers to tackle the most difficult, dangerous and dirty tasks, leading to higher production, better quality, and ultimately increased profitability.